Sustainable Cooling
Our commitments, projects and solutions for planet's sakeUseful technologies to reduce energy use, water use for industrial cooling, and CO2 emissions to the atmosphere.
1. Our best practices and technologies for sustainable cooling
Every industry sector and every company today is called upon to do its part to develop an increasingly circular economy and take care of our planet. These are some best practices that we believe are necessary and consistent to talk about sustainability, sustainable cooling and energy efficient cooling systems:
- since 2011, 65 percent of the energy used in our Siziano (PV) plant has been self-produced from alternative sources;
- Having achieved ISO 14001 certification. We work with an appropriate management system to keep the environmental impacts of our activities under control, systematically seeking improvement;
- manage cooling water (mainly in production settings), always in a “circular” manner, reducing its consumption and reusing available resources;
- use water always respecting its natural cycle;
- act every day as cooling consultants, suggesting the technological solution (air, adiabatic and evaporative cooling) that is efficient and sustainable in the context in which it is to be placed, significantly reducing water, energy and footprint;
- Being able to determine and provide the “carbon footprint” of each of our products. We also work to reduce environmental impact through careful selection of materials that can promote product lifetime and end-of-life recycling;
- Having activated an internal process to promote remanufactured products with low environmental impact through the application of circular economy principles.
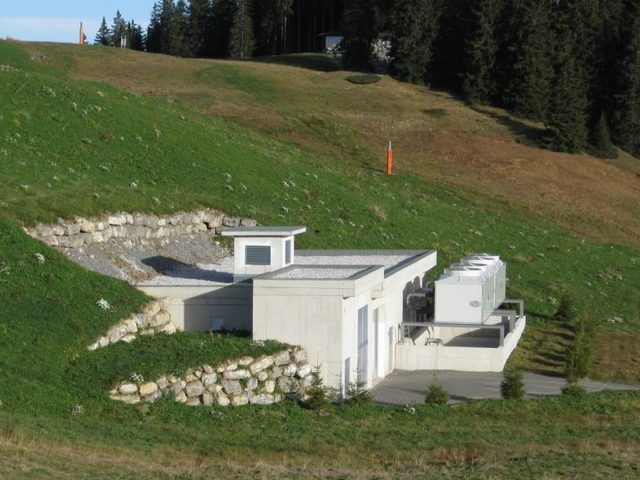
2. We use water in a "circular" way, respecting its natural cycle
Water is the process fluid that we have been cooling since 1960, as well as being the useful element for increasing plant efficiency. We manage water in a circular way, that is, by suggesting solutions for its use and subsequent recovery, according to the following scheme:
The water cycle in adiabatic cooling
- Approximately 0.2 percent of the mass to be cooled evaporates, thus returning to the environment (typically in medium-hot periods a specific section is sprayed with water to reduce the air temperature).
The water cycle in evaporative cooling
- About 2% of the mass to be cooled evaporates, thus returning to the environment.
- About 1 percent of the mass to be cooled is disposed of in the network to maintain the correct concentration of salts in the circuit. The determination of this value is closely related to the quality of the treated water.
- For more information you can read this article.
In terms of the following schematic, however, the systems proposed by MITA Cooling Technologies are located within the boxes highlighted in red. Instead, wastewater treatment (part highlighted in yellow) is handled by another company with which MITA Cooling Technologies collaborates: MITA Water Technologies (www.mitawatertechnologies.com). The goal is to make human use of the water resource as close as possible to the natural water cycle.
3. We also offer remanufactured systems and work on carbon footprint reduction
We are focusing on a careful choice of materials to be used in the construction of our machines: this is through research into components that encourage recycling at the end of their life: this is also how we can provide green cooling solutions. All this also involves the involvement of our suppliers. The goal is threefold:
- reduce the energy used in their production,
- increase the renewable component (self-produced or purchased),
- increase the second raw material component.
In addition, we provide remanufactured cooling systems: a new offering, sustainable for the environment and beneficial for the customer due to the lower use of energy and raw materials.
Not only that. Upon request, we can provide add to the analysis of the most optimized solution also the carbon footprint impact: all projects can be accompanied by LCA analysis, electricity use and water use.
We suggest PLC management (inverter system) for all machines for savings in the order of 80 percent over lifecycle. In addition, complete water treatment systems are undoubtedly a good practice.
Ask for information Find out the service of remanufactured coolers4. How we select the most sustainable cooling solution
We analyze and select the most suitable solution and service to improve the environmental impact in cooling production processes, including with the support of advanced comparison and optimization softwares.
Each solution, if selected carefully and according to project needs, can bring savings in resource use and be environmentally sustainable and cost-effective.
Here’s how.
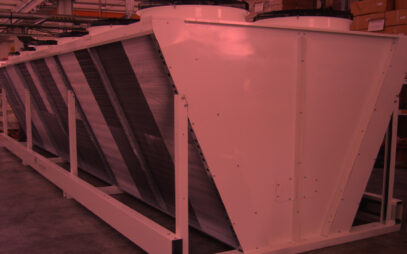
Dry Cooler
- No use of water to facilitate heat transfer (i.e., cooling of the process fluid).
- 100% use of electricity to move air (the only cooling carrier) through one or more fans.
- It is among the product categories that MITA is able to regenerate.
- Indication of “carbon footprint” by the MITA team.
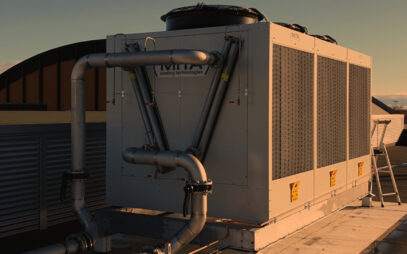
Adiabatic Dry Cooler
- Minimal use of water (only for adiabatic operation), which is useful for facilitating heat transfer (i.e., cooling of the process fluid).
- Optimized energy use (higher efficiency due to adiabatic supply).
Smaller installation spaces compared to the 100% air solution. - It is among the product categories that MITA is able to regenerate.
- Indication of “carbon footprint” by the MITA team.
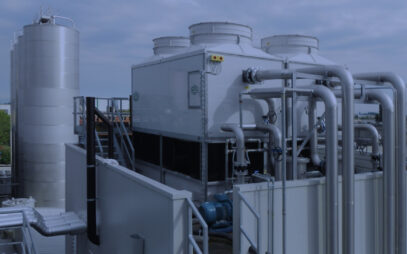
Evaporative Cooler
- Use of water for efficient heat transfer (i.e., cooling of the process fluid.
- Low and further optimizable energy use.
Extremely small installation spaces. - Falls within the product categories that MITA is able to regenerate.
- Indication of “carbon footprint” by the MITA team.
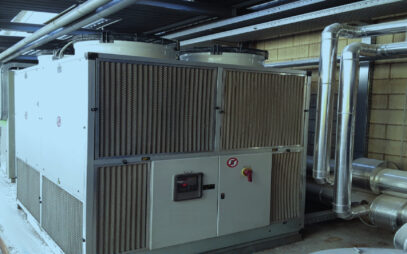
Industrial Chiller
- Use of electrical energy only for refrigerant gas compression and the use of one or more fans for the refrigerant condensing phase (in the case of air-cooled machines); possibility of “free-cooling” solutions.
- Use of electricity for refrigerant gas compression and water for the condensing phase of refrigerant gas (in the case of water-cooled machines).
- Extremely small installation spaces.
- It is within the product categories that MITA is able to regenerate.
- Indication of “carbon footprint” by the MITA team.
Discover the sustainability of our energy-efficient coolers
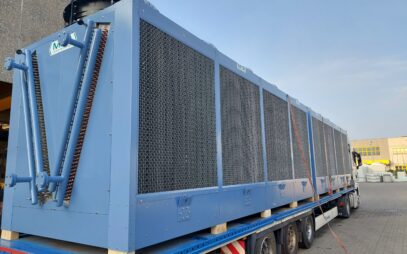
PAD-XL W Adiabatic Cooler
Ideal for those who want to use very little cooling water while eliminating its management, or as an alternative to the classic dry cooler, especially with performance in the hottest times of the year in mind.
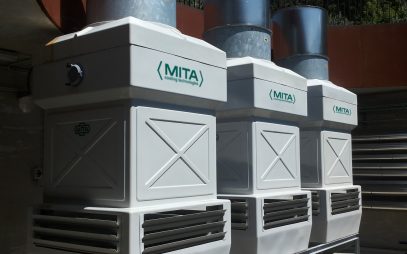
PMS Evaporative Open-Circuit Cooling Tower
It is a cooling tower for industries of any type and for any water quality: very compact, self-supporting, light and long-lasting non-corrodible fiberglass structure.
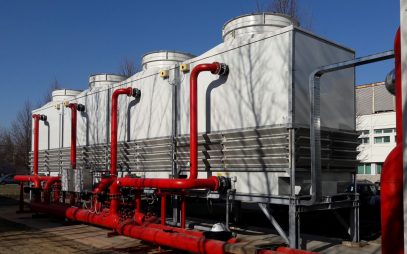
PME-E Open-Circuit Evaporative Cooling Tower
A light and non-corrodible open-circuit evaporative cooling tower: process industry and HVAC operators will be able to count on its multiple versions and ease of transport and installation.
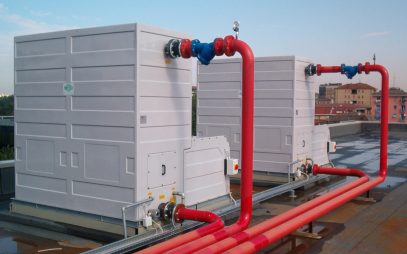
MCT Open-Circuit Evaporative Cooling Tower
Compact design and reduced dimensions: a range of evaporative cooling towers with centrifugal fans for special space configurations. MCT-EC version available with electronically controlled fans.

MCC Closed-Circuit Evaporative Cooling Tower
Some industries need to keep the chemical-physical characteristics of the process fluids unchanged: in these cases, MCC closed-circuit evaporative cooling tower joins the game. Possibility to work in free-cooling mode. MCC-EC version available with electronically controlled fans.
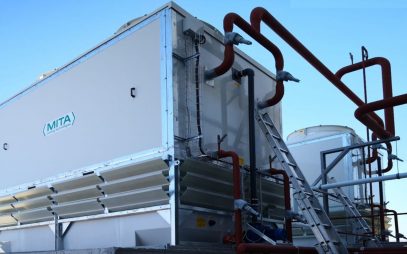
MCE Evaporative Condenser
Compact, efficient and easily accessible: MCE evaporative condenser ensures refrigeration operators all the operating standards of its own technology class. The typical MITA evaporative coolers’ durability over time is a plus. MCE-EC version available with electronically controlled fans.
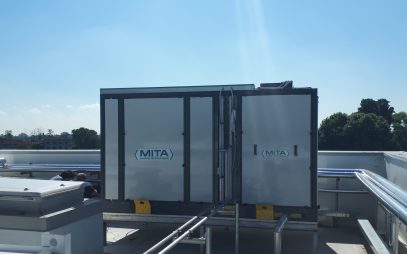
Alchemist Adiabatic Sucooler
Performance, savings and environmental sustainability thanks to a patented Plug & Play subcooler for refrigeration systems working with R744 (CO2) and fluorinated refrigerants (HCFC, HFC, HFO).
Do you wish to have free advice?
Contact Us NowYour Plant Needs
Tools to help you choose
Preliminary plant evaluation
Tailor-made design
Newsletter
Subscribe to MITA newsletter and stay updated on technical solutions for industrial and civil cooling and get to know our offer.