Dry Coolers: Complete Guide to Industrial Air Cooling
An article discovering a simple cooling technology in high demand by customers in industry and civil air conditioning: dry coolers, or dry cooling systems. We are talking about solutions with low acquisition cost and low maintenance requirements, but which require specific output temperatures of the fluid to be cooled and sometimes large installation spaces.
So let’s take a detailed look at what dry coolers are, how they work, and what they look like.
1. Introduction to Dry Coolers
Dry coolers are based on a simple but effective principle: convection cooling. As outside air is conveyed and pushed by one or more fans, it passes through “finned coils” located inside the dry cooler, absorbing heat from the process fluid flowing through it. The air is then expelled into the environment, completing the cooling cycle.
A few notes on terminology before continuing. Dry coolers are also often referred to as air coolers, due to their characteristic of operating solely with air as the carrier; the terms are therefore interchangeable. It is also not uncommon to read the term dry cooling system.
2. Structure and components of dry coolers
Dry coolers consist of relatively simple components that are effective in working together to dissipate heat.
- Closed circuit with finned coils. The heart of the dry cooler is a closed circuit that contains/runs the process fluid that is to be cooled. This fluid flows within coils of tubes connected together (via welded bends) and inserted into a series of “fins,” which are thin plates that form a “finned pack” (finned coils).
- Metal fins on the surface of the coil increase the heat exchange surface area with the air, maximizing cooling, that is, the transfer of fluid heat to the external environment. Materials, thicknesses and geometries of finned coils are defined according to the characteristics of the fluid to be cooled and specific requirements.
- Fans. Powerful fans draw air from the environment and push it through the finned coils. The speed and airflow rate of the fans are critical to ensure effective cooling of the fluid.
- Motor. Running the fans is one or more electric motors. Modern dry coolers use high-efficiency motors to reduce energy consumption and keep noise down.
- Frame and structure. The frame and structure of the dry cooler must be weatherproof and provide protection for the internal components. They can be made of galvanized or painted steel to resist corrosion.
3. Advantages of dry coolers
There are a number of benefits to adopting dry coolers.
- Simplicity of construction, installation and start-up. It is evident from the description that these are machines that do not require special ancillary work to assemble (exclusive of grounding and necessary electrical and hydraulic connections).
- Low maintenance. The robust but simple design of dry coolers requires very little intervention, ensuring low operating costs in the long run.
- Air only. The operation of this technology requires nothing but outside air, as we have seen moved by one or more fans. Of course, this could translate into a limitation for those applications that require precisely lower fluid temperatures to cool than outside air.
- Low operating costs. This is of course an effect of the previous functional characteristics.
- Installation flexibility. Dry coolers can be installed outdoors or indoors, adapting to different plant layout requirements. Their modularity also makes them suitable for retrofitting existing plants.
- Versatility of operation. Systems with dry coolers can operate throughout the year, without problems referred to low surrounding temperatures.
4. Output temperatures and power calculation of a dry cooler.
Since the dry cooler uses only air as the cooling carrier, this industrial system can structurally achieve output temperatures no lower than the air’s dry bulb temperature (i.e., the temperature of the outside air): this is something to always keep in mind in order to know whether this is the solution we need. The consequence of this is that the dry cooler becomes the optimal solution if it is sufficient to obtain a medium to high temperature fluid output, especially if we think about the warmer seasons and if we do not want to use water as a cooling “tool”.
So how to size a dry cooler correctly? How to correctly calculate the required capacity? Several factors come into play.
It is critical to select a dry cooler with the appropriate air flow rate and heat transfer surface area for the amount of heat to be dissipated by the fluid. Factors such as the temperature and volumetric flow of the process fluid, the ambient temperature, and the desired temperature difference at the outlet play a key role in sizing the dry cooler.
We have also seen that dry coolers are able to lower the temperature of the process fluid close to the ambient air temperature.
Sizing a dry cooler is a process that requires careful evaluation of several factors to ensure that the selected unit will meet the specific needs of the application.
The main steps are as follows.
- Thermal load calculation. It is necessary to determine the precise amount of heat that the dry cooler will need to dissipate. This depends on factors such as the type of fluid to be cooled, its inlet and outlet temperatures, and environmental conditions.
- Determining the air flow rate. Once the heat load is known, the amount of air required to remove that heat is calculated. This value is obtained through the desired temperature difference between the air entering and leaving the dry cooler.
- Selection of dry cooler. Based on the calculated heat load and air flow rate, the most suitable dry cooler model is selected. Factors such as air pressure drop, air velocity, heat transfer rate, and finned coil materials, thicknesses, and geometries are considered.
In addition to these elements, others must be taken into account in order to correctly size and calculate the required power of a dry cooler: available space, noise levels required for proper operation (considering the civil or industrial context of the installation), needs related to future maintenance of the system…
The variables, as can be seen, are many. As in any case, a good process cooling advisor is, however, able to orient the client by asking the right questions about his or her needs. There is also specific software that, considering application parameters, helps the professional simulate its performance in terms of fluid outlet temperature and define the most suitable dry cooler model.
5. Types of dry coolers
There are a few types of dry coolers: horizontally arranged, with the typical “table” shape, and vertically arranged, or V-shaped. In addition, air coolers can increase their efficiency by mounting adiabatic pre-cooling devices.
Let’s look at these three types in more detail.
Ask for Information- Table-type dry coolers. A horizontally placed finned coil characterizes these systems with fans that draw air vertically. Industrial dry coolers and condensers with this layout have the typical flat configuration. The main advantage lies in the fact that they can be raised to maximize lower airflow space, with minimal space for air circulation.
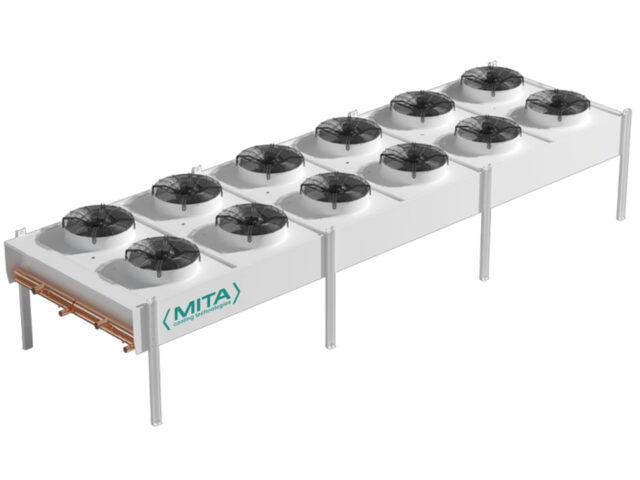
- V-type dry coolers. They feature a V-shaped configuration formed by two inclined finned coils, with centrally positioned fans that draw in and push air through the coils. This allows a larger exchange surface area and greater air flow rate: maximum surface area per footprint for greater heat removal.
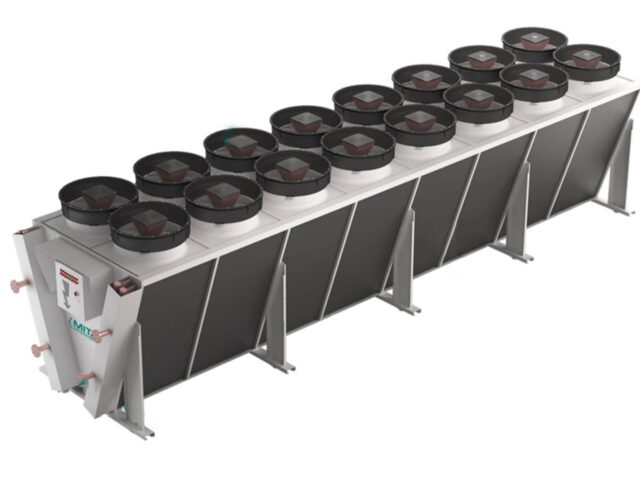
- Adiabatic dry coolers. This is a device in which air, during hot periods of the day and year, can be pre-cooled by cycles of wetting with water. This allows for greater efficiency, considering of course having to “manage” water. But we will see below the working principle of this variant of air cooler.
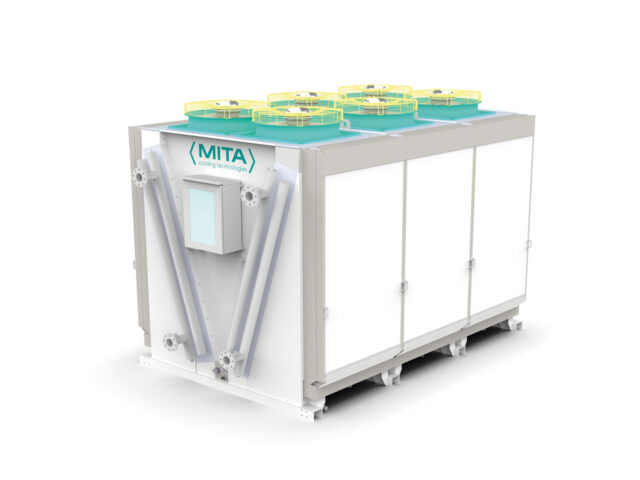
6. Sostenibilità, efficienza energetica e riduzione del rumore coi dry cooler
Let’s make a necessary premise: any type of industrial cooler, including air coolers, can bring efficiency (lower resource use and lower environmental impact) if selected and configured correctly by the manufacturer and supplier. How can this be achieved? By knowing precisely the design data of the plant to be served and its unique needs of required performance and available resources. Today this task is facilitated by advanced selection, configuration and optimization software.
That said, a number of points can be brought to attention for having efficient dry coolers.
- Energy-efficient components: high-efficiency motors and fans, often electronically controlled, that minimize resource use.
- Material selection: an awareness by the manufacturer of the recyclability of the materials used, or their end-of-life management, helps reduce the environmental impact of our air cooler.
- Operational efficiency: proper maintenance and cleaning of dry coolers ensures optimal airflow and heat transfer, reducing energy consumption. Of course, this step is the responsibility of both a good manufacturer and consultant, who can best advise the customer, and of the customer himself and the good organization of his internal operations.
7. Dry cooler vs. other cooling systems
Dry coolers are certainly not the only systems for heat dissipation in industrial processes.
The question of what is the best cooling system to use to cool fluids (water and glycol or other fluids) for use in manufacturing processes is a great classic. Manufacturers and consultants typically respond with another classic answer: it depends. Because the best cooling system does not exist and instead one must know and compare the different structural advantages of chillers, evaporative cooling towers, adiabatic dry coolers, and “standard” dry coolers.
Again, we then make a comparison on how dry coolers work compared to other heat dissipation systems.
7.1. Dry cooler vs. chiller
Here is a classic example of contrasting different cooling systems: better a dry cooler or an industrial chiller?
It is clear that we must start with the output temperatures allowed by the two systems. In this sense, a chiller (“mechanical cooler”) can achieve output fluid temperatures well below room temperature, even below 0 °C. A dry cooler, on the other hand, is more suitable, as we have already seen, for medium to high output temperatures (in warmer seasons) or at least close to those of the outside air. It is in fact a system that cannot structurally go below the dry bulb temperature of the environment.
But what if the demand is for intermediate outlet temperatures, for example, between 20 and 30 °C? In this case, more attention must be paid to the other design factors and needs of the system to be served.
A further point to be made is about the structure and components of the two systems. An air cooler is a simple piece of machinery, consisting essentially of a heat exchange coil and a motor-fan assembly. On the other hand, a chiller or refrigeration unit is a much more complex system that must leverage an entire refrigerant circuit to achieve its high performance.Such a solution generates much higher acquisition and operating costs and requires more maintenance.
To optimize energy use and provide flexibility, it is still possible to combine dry cooler and chiller-a solution that has seen some growth in recent years. For example, one can use the dry cooler during colder times of the year and the chiller during warmer periods, or use the dry cooler as a pre-cooler to reduce the load on the chiller. Not to mention that there are so-called free-cooling chillers, which function as dry coolers during cold periods, allowing compressors to be turned off and saving energy.
For your convenience, here is a useful and necessarily simplified primer on the most important factors to consider in evaluating an informed choice: dry cooler vs. chiller.
- Operating temperature. If a very cold fluid is required (e.g., 10 °C or lower), the chiller is the only option between the two. For higher temperatures (20-30 °C), both solutions can be evaluated.
- Installation spaces. Where space is limited, the chiller may be the optimal choice.
- Environmental conditions. In hot and humid climates, the efficiency of a dry cooler may decrease. A chiller unit, on the other hand, is less affected by outdoor conditions.
- Dry coolers generally have lower investment and operating costs than the competing solution.
- Energy efficiency. Energy efficiency depends on several factors, including ambient temperature, fluid outlet temperature, and the technology used.
- Dry coolers require less maintenance than refrigeration units, which have more complex components.
7.2. Dry cooler vs. cooling tower
In terms of operating result, the main difference between a dry cooler and an evaporative cooling tower lies in the fact that the former has in the dry bulb temperature of the air (the outside air temperature) the minimum limit for the output temperature of the cooled fluid. In contrast, the cooling tower can get close to the wet bulb temperature (approximately 10 °C below the outdoor temperature).
There is a precise formula for calculating the wet bulb temperature (Tw) given the dry bulb (Ta), as well as several online calculators. Suffice it to say that Tw is always lower than Ta at less than 100 percent relative humidity: this underscores the greater efficiency of the cooling tower compared to the dry cooler. An element to consider when choosing the best cooler.
On the other hand, in terms of resource use, the cooling tower requires water for its operation where the dry cooler, by definition, does not use this resource for its operation.
Are performance (and the thermal jump to be achieved), space available for installation, or water savings more important for the system to serve? The answer to this question definitely begins to tilt the choice: dry cooler if the focus is on water savings, cooling tower if the greater need lies in performance and smaller available installation space.
7.3. “Standard” dry cooler vs. adiabatic dry cooler
Recall the structural differences between the two systems. A standard dry cooler works through a simple principle: the fluid to be cooled (usually water or water and glycol) is pumped through a series of pipes inside a unit. Outside air is forced through fins adjacent to the pipes, absorbing heat from the fluid and cooling it. This process occurs without the use of evaporation water. A dry cooler with an adiabatic device is a more advanced system that combines standard dry cooler technology with an adiabatic cooling process (which can be used at certain times of the year or day): in this case, the outside air is pre-cooled with water wetting cycles before making contact with the finned coil.
The fluid output in an adiabatic dry cooler can fall below the dry bulb temperature of the air (though not the wet bulb temperature). In contrast, a standard dry cooler cannot structurally achieve this. This difference is in itself a discriminating factor if the system to be served needs to dissipate heat at levels slightly above or slightly below this threshold, or some “guarantee” of performance is needed even on the hottest days or hours of the year.
The adiabatic dry cooler can also operate in standard mode, i.e., air-only and without a water pre-cooling device, if this is sufficient in certain seasonality-this is, of course, a point in favor of this equipment.
8. Applications of dry coolers
The same applies as for other industrial cooling systems: dry coolers can be included in the most diverse types of civil and industrial installations, as long as the temperature and capacity requirements of the individual project are known.
As examples, here are some installation contexts.
- Industrial processes: liquid cooling in power plants, chemical processing, plastic production, metal processing, food and beverage.
- HVAC systems: heat disposal in commercial and industrial buildings to maintain air conditioning.
- Datacenter: the purpose, of course, is to maintain optimal operating temperatures for servers.
9. Focus: dry coolers for data centers
Let’s focus for a moment on the last item on the previous list: data centers are one of the environments where cooling technologies are required and, possibly, using a limited amount of resources.
We are talking in this case about server room cooling with dry coolers for data centers, an application that is also booming in view of investments in artificial intelligence. These are also environments in which business continuity and thus machine reliability are critical.
Dry coolers can serve these types of systems-the choice of these systems among other cooling technologies always lies in the specifications of the individual project. Of course, as we have already seen dry cooler is the optimal solution in cold climates or where the temperature of the fluid to be cooled may be close to or higher than the outside air temperature.
There are excellent case studies of the use of dry cooler systems in all three versions: table-top, V-configuration, and adiabatic device.
Dry cooler may not be the most suitable technology if, on the contrary, we are in a very hot climate and/or where there is the possibility of using water as a cooling resource.
10. Dry Cooler Manufacturers: how to evaluate them
We come to the question that every customer in the civil or industrial sector asks, even in reference to other technologies: how to select the right dry cooler manufacturer?
The criteria can be the most diverse and subjective. However, it is worth considering some of them.
- Width of range. Given that, as we have seen, one technology is not always the best in an absolute sense (and the same is true for air cooling systems), being able to count on a diverse range of solutions increases the possibility of choosing the one that is tailored to our system.
- Product differentiation (within the same category). We have seen that there are different types of dry coolers, each with its own functional advantages.
- Advice and service. In some situations, the “intangible” part of the sale is even more important than the “tangible” part: are the manufacturers we selected in our short list following us as consultants? Will they carry out custom design for us? Will they follow us in the installation phases and be available in the physiological maintenance phases in the future?
- Company history and references. They are, of course, an indication of the supplier’s experience and professionalism: again, this should be evaluated carefully.
MITA Standard and Adiabatic Dry Coolers
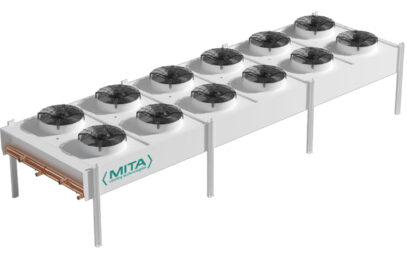
MDC-F Table-Type Dry Cooler
No use of water, extreme simplicity of operation: these are the advantages of dry coolers in general and, in particular, of the MDC series with table coil configuration. MDC-F is an excellent solution for medium to high outlet fluid temperatures.
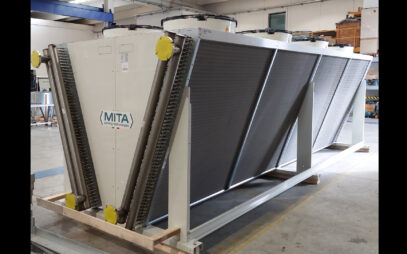
MDC-V V-Type Dry Cooler
Ease of installation, operation and maintenance–serving even large systems: this is the MDC-V V-shaped dry cooler. The peculiar design of the coils allows a larger heat exchange surface area than table-top dry cooler systems. All in an easily scalable solution.
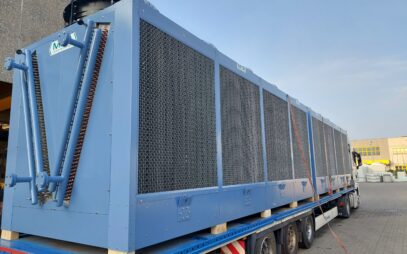
PAD-XL W Adiabatic Cooler
Ideal for those who want to use very little cooling water while eliminating its management, or as an alternative to the classic dry cooler, especially with performance in the hottest times of the year in mind.
Resources
Best practices
Read all Pieces of Advice by MITA Cooling TechnologiesWhat to Know
Find Out All Technical TermsTechnical Articles
Read All our Technical ArticlesNewsletter
Subscribe to MITA newsletter and stay updated on technical solutions for industrial and civil cooling and get to know our offer.