Closed-Circuit Cooling Towers: 3 Reasons why to Choose Them
Do you want to know why you should choose a closed-circuit cooling tower, even known as closed-loop cooling tower? Here below you can find three reasons why to choose them.
When we talk about cooling machines, we are used to think about the typical open-circuit cooling tower, an evaporative cooler operating through a direct contact between air and water. Nevertheless, this is not always the best solution for civil and industrial plants: in some projects it could be better to avoid a direct contact between the air and the water (hydraulic separation) and, therefore, a closed-circuit cooling tower can be preferred.
What are closed-circuit cooling towers?
Let us see what closed-circuit cooling towers are and how they work. Basically speaking, they exploit the same evaporation principle of open-type coolers: the forced evaporation of a minimal quantity of water lowers temperature of the main water mass.
Closed-loop cooler has two separate fluid circuits:
- one in which the fluid is recirculated inside smooth tube coils (primary circuit),
- one where recirculating water (secondary circuit) is sprayed on top of the coils.
The contact between air (drawn by the fans) and sprayed water provides evaporative cooling similar to an open circuit cooling tower, except that process fluid is never in direct contact with the air (hydraulic separation).
Tell Us Your NeedsThree reasons why to choose closed-circuit cooling towers
Now we know the basic elements and we can better understand the 3 advantages of closed-circuit cooling towers.
- No contamination of the primary circuit. Many civil and industrial processes require to maintain the process fluid uncontaminated by the external environment: for instance, this is true for most of food production processes. Closed-circuit cooling towers, grant this need: in effect, coils separate process fluid from ambient air drawn in by the fans, keeping it clean and uncontaminated in a closed loop.
- Reduction of freezing risk. Since the process water circulates in heat exchange coils and never gets in contact with air, glycole can be added to it to lower the fluid freezing point. This can be a big advantage especially in cold countries (in e.g. Scandinavian countries, Russia, Canada, …) where temperature frequently goes below zero.
- A simpler system. A closed-circuit cooling tower can be an alternative to a system composed by an open circuit cooling tower and a heat exchanger. This leads to some advantage:
- Easier plant layout
- Reduced footprint
- Higher thermal efficiency
Conclusions
“There is no best cooler in absolute terms”, says the wise cooling advisor: this means that not always a closed-circuit cooler should be preferred to other solutions. Nevertheless, some project requirements can strongly make us opt for its use.
We have listed some advantages (related to the preservation of the liquid to be cooled) that make closed-circuit cooling towers reliable in certain situations – and according to specific project requirements.
Contact Us and Find All MITA Technologies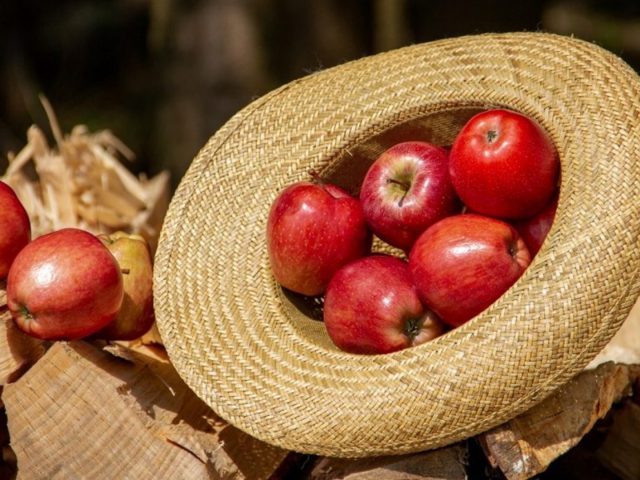
Cooling Technologies for a High-Quality Food Process
More than a hundred years ago it was an apple orchard: now it is one of the most important food industries in Sweden. This is the company to which MITA Cooling Technologies and CAMPreq have provided solutions-as manufacturer and process cooling consultant, respectively.
Learn MoreResources
Best practices
Read all Pieces of Advice by MITA Cooling TechnologiesWhat to Know
Find Out All Technical TermsTechnical Articles
Read All our Technical ArticlesNewsletter
Subscribe to MITA newsletter and stay updated on technical solutions for industrial and civil cooling and get to know our offer.