Significant energy savings. Up to 80% energy cost savings by free-cooling mode, reducing the load on compressors.
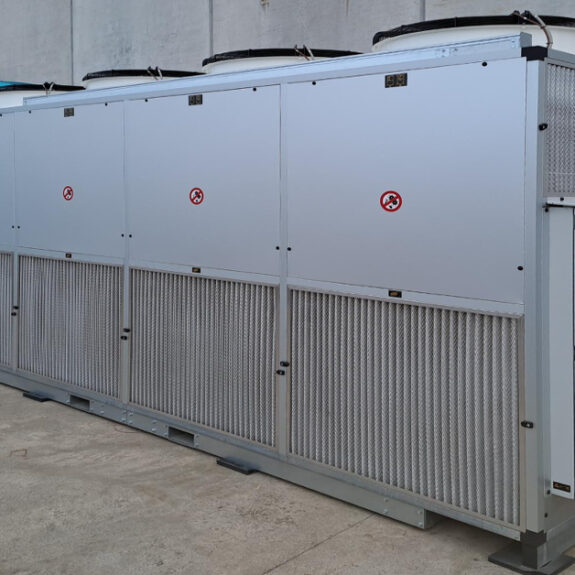
RW / EFC ax Chiller with Free-Cooling
energy saving and performance optimizationThe RW / EFC ax chiller combines energy efficiency and sustainability for industrial refrigeration with integrated free-cooling technology. The combination of operating modes, between free-cooling and compressor operation, allows up to 80 percent energy savings compared to conventional versions.
Efficient at very low temperatures. The lower the outdoor air temperature, the higher the efficiency of the machinery: with a temperature difference greater than 5°C, free-cooling operation is able to completely shut down the compressors.
Customizable and integrable configuration. Turnkey solution that integrates with other systems and components: a single point of contact for the entire refrigeration system.
Optimized resource management. Brushless EC fans ensure precise control, reduced compressor operating hours, and reduced energy consumption as a result.
Durability of the system. Less use of compressors ensures an increase in the lifetime of the entire system.
Remote monitoring arranged. Different types of IoT services are available.
Chiller with Free-Cooling: description and operation
The RW / EFC ax chiller from Frigofluid, a partner company of MITA Cooling Technologies in MITA Group, is designed to provide efficient industrial cooling through a combination of operating modes.
In fact, the structure of the system allows it to automatically manage three operating modes depending on the season and ambient air temperature:
- Summer mode. With outdoor temperatures above 23°C, the chiller uses only the compressors to maintain fluid temperature, ensuring maximum cooling performance even during the hottest periods.
- Intermediate mode (partial energy saving). When the ambient air varies between 15°C and 23°C, the system combines the action of the compressors and the free-cooling section. This provides partial energy savings by using the cooler air to reduce the compressor load.
- Winter mode (total energy saving). At temperatures below 15°C, the chiller relies solely on the free-cooling section. Cool outside air is used to cool the fluid without compressor operation, ensuring low energy consumption operation.
This technology, which integrates the operation of a chiller with that of a dry cooler, exploits free-cooling separately from the refrigeration circuit, improving operating efficiency and extending component life.
This advanced configuration makes the RW / EFC ax chiller a sustainable and cost-effective solution for industrial cooling needs, reducing environmental impact and improving the energy efficiency of the entire plant.
Ask for InformationTechnical Specifications
Design data.
- Rated thermal power: 60 to 230 kW. Possible power increase with chiller plus dry cooler systems sized by Frigofluid.
- Fluid temperature range: 10°C to 25°C.
- Ambient temperature: up to 40°C (special configurations available).
Types of storage available.
- RWC ax: hermetically sealed internal storage (possibility of connecting other central units in parallel).
- RWA ax: internal storage at atmospheric pressure.
- RWE ax: for external storage.
Do you need info?
Ask for Information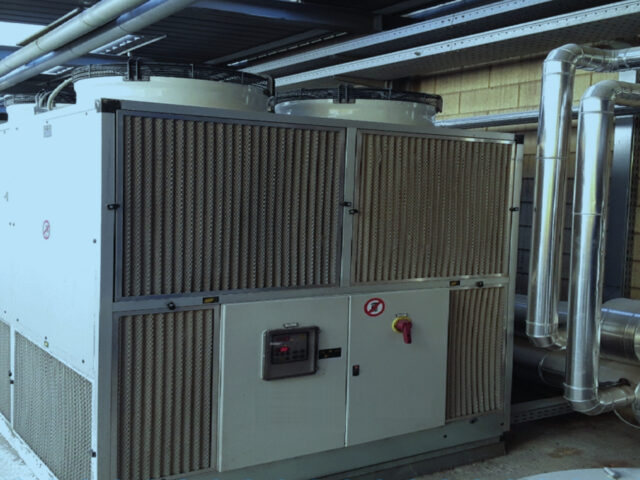
Environmental and economic sustainability of the industrial chiller
- Use of electrical energy only for refrigerant gas compression and the use of one or more fans for the refrigerant condensing phase (in the case of air-cooled machines); possibility of “free-cooling” solutions.
- Use of electricity for refrigerant gas compression and water for the condensing phase of refrigerant gas (in the case of water-cooled machines).
- Extremely small installation spaces.
- Falls within the product categories that MITA is able to regenerate.
- Indication of “carbon footprint” from the MITA team.
Some MITA projects
Closed-Circuit Cooling Towers for Engine Test Bench
MITA built the cooling system for the electronically controlled hydraulic test bench at the Experimental Institute for Agricultural Mechanization (ISMA) in Treviglio: an MCC C series closed-loop evaporative tower. Among the benefits brought by the plant are reduced operating costs and water use.
Learn MoreCooling Towers for Bologna Hospital
The Major Hospital "Pizzardi" of Bologna installs as many as 12 non-corrodible and easy-to-maintain cooling towers to support the refrigeration units for the air conditioning system: performance and attention to noise level.
Learn MoreCooling Towers and Sand Filters for Chemical Plant
At the Pogliano Milanese plant of Clariant Masterbatches, MITA built a cooling system for the extruding process that uses exchangers combined with several evaporative towers. In addition, MITA Water Technologies supplied a continuously regenerating sand filter that keeps the cooling water clean.
Learn MoreApplications served
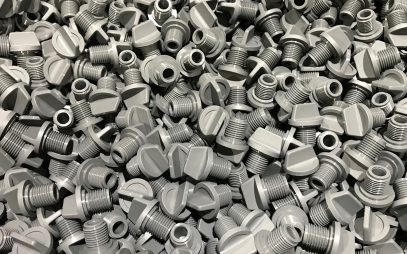
Plastics and Rubber
Plastic and rubber processing requires specific cooling processes to ensure high productivity, finished product quality and temperature control during molding, extrusion and mixing. MITA Cooling Technologies offers advanced solutions-from chillers to adiabatic cooling systems-that optimize the cooling of molds, hydraulic components and oils, ensuring reliability and energy savings.
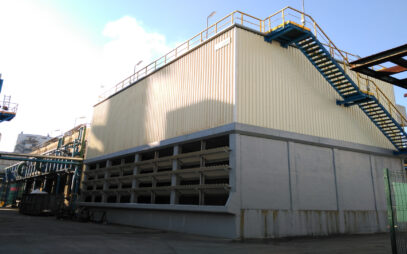
Metalworking
Metal processing requires reliable, high-efficiency cooling systems to maintain stable temperatures during processes such as casting, rolling, and stamping. MITA Cooling Technologies offers advanced industrial cooling solutions: evaporative towers, dry coolers, adiabatic systems supported by parameter control panels. Reliability, precision, resource optimization: the cooling systems the metal processing industry needs.
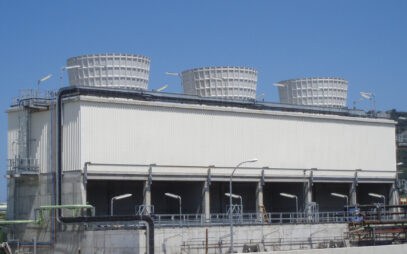
Oil & Gas
MITA Cooling Technologies provides robust and efficient cooling solutions for the oil & gas industry. They are also optimized for intensive process cooling needs and resistance to extreme operating conditions. The PMM and PME-XL modular towers, together with the PU field-mounted towers, address the need for high flow rates, ease of installation and maintenance in complex environments, ensuring high performance and operational continuity even in harsh environments.
Tools to help you choose
Cooling Advisors
Preliminary plant evaluation
Tailor-made design
Your Plant Needs
Newsletter
Subscribe to MITA newsletter and stay updated on technical solutions for industrial and civil cooling and get to know our offer.